Noi di Rubino
Rubino & Reaktive rendono digitale il processo di produzione di Rinaldi Group
Smart Manufacturing: un gioco di squadra agevolato dal Piano Nazionale Industria 4.0
Si tratta di un importante progetto di Smart Manufacturing, che abbraccia i più moderni modelli di fabbrica connessa, nato da un gioco di squadra sinergico tra Allnet.Italia S.p.A., Rubino S.r.l. – azienda specializzata nel settore dell’etichettatura e delle tecnologie di stampa – e Reaktive S.r.l. – system integrator con specifiche competenze IT in processi di digitalizzazione. Una soluzione all’avanguardia che, rispettando gli otto pillar previsti dal Piano Nazionale Industria 4.0, prevede l’integrazione delle tecnologie RFID di nuova generazione firmate Impinj all’interno dei processi produttivi di Rinaldi Group, al fine di accrescere la sua efficienza e la competitività nel settore del bedding.
Da oltre 50 anni l’Azienda disegna, progetta e realizza, anche per conto terzi, materassi unici ed esclusivi che coniugano design Made in Italy e innovazione continua applicata non solo al prodotto ma anche al processo. Una visione strategica che la conduce ad investire costantemente in attività di R&D e a stringere importanti collaborazioni, come quella con l’Università di Salerno per lo studio e lo sviluppo di esclusivi principi di ergonomia e comfort del sonno.
Dal Barcode al RFID: il passaggio fondamentale della scelta della tecnologia
“Un primo tentativo di realizzare un sistema di tracciamento della produzione tramite RFID fu realizzato proprio a seguito di uno studio commissionato al Dipartimento di Ingegneria Industriale dell’Università.” interviene l’Ing. Giuseppe De Vivo, IT Manager di Rinaldi Group che racconta: “Tra le varie tecnologie individuate, si scelse di perseguire la strada dei barcode. Il progetto però non andò a buon fine poichè si generavano delle interferenze con le gabbie in ferro dei magazzini verticali posti sopra alcuni centri di lavorazione.” e continua: “Quando siamo entrati in contatto con Rubino per la richiesta di una stampa personalizzata di etichette in quadricromia su tessuto, ci siamo trovati ad approfondire nuovamente l’argomento. La determinazione e la propositività dimostrata dall’azienda lo ha reso, fin da subito, un partner ideale. Il team di Rubino, infatti, dopo un’analisi preliminare ha realizzato un sopralluogo in stabilimento e ha testato alcuni sistemi, allo scopo di individuare tutti i punti critici inerenti i nostri processi produttivi. Un approccio che abbiamo molto apprezzato unitamente alla vicinanza territoriale, all’elevata professionalità, ad un’offerta completa con un eccellente rapporto qualità/prezzo e, non ultimo, alla collaborazione con un pool di società altamente qualificate, come Allnet.Italia e Reaktive.”
“Il gioco di squadra generato con Allnet.Italia e Reaktive è stato determinante per il successo del progetto, sia nell’individuazione delle tecnologie più adeguate, sia nell’integrazione delle stesse con i sistemi della Rinaldi Group.” Interviene Giuseppe Rubino, Responsabile Tecnico e Commerciale di Rubino S.r.l. che continua: “Nello specifico, Allnet.Italia ci ha accompagnato, lungo ogni fase di questa trasformazione digitale, con un’attività di consulenza tecnica costante. Il risultato è un’infrastruttura completa realizzata con le soluzioni intelligenti IoT di Impinj. In tal senso abbiamo molto apprezzato l’elevato livello di competenza dimostrato dai membri della BU Internet of Things, anche nella risoluzione di sfide progettuali emerse in corso d’opera.” e conclude: “L’expertise di Reaktive, invece, si è rivelata fondamentale per permettere ai dispositivi di Impinj di dialogare con i software di produzione interni dell’azienda, per la raccolta, lo scambio e l’analisi dei dati dell’intero processo. Grazie a loro supporto è stato possibile ampliare la memoria dei Tag, attraverso la creazione di un sistema in cloud che permette di salvare le informazioni sul database virtualizzato di Rinaldi Group, assicurando molteplici vantaggi in termini di riduzione dei costi, velocità di lettura e abbattimento del rischio di contraffazione.”

“La piattaforma RAIN RFID di Impinj è una delle più complete e offre un unico set integrato di elementi Hardware e Software.” Spiega Ilario Dino Gaudioso, Sales Account di Allnet.Italia che aggiunge: “In particolare, nell’ambito del progetto di smart manufacturing di Rinaldi Group abbiamo utilizzato un sistema composto da Tag Chip, circa 14 Antenne, 4 Reader Chip, 4 cavi Impinj AC Power Supply w/o e un Software, assicurando al cliente prestazioni di connettività senza eguali. Tale soluzione è calibrata sulle attuali esigenze produttive dell’azienda ed è perfettamente scalabile in qualsiasi momento. La possibilità di tracciare il percorso di ogni singolo materasso lungo l’intero processo, dalla fase di ingresso delle materie prime in azienda, fino all’imballaggio per la consegna della merce in negozio, assicura una qualità di prodotto superiore, grazie all’automazione di alcune fasi di lavorazione, con molteplici vantaggi anche in termini di efficienza e competitività.”
La prima ottimizzazione avviene già in fase di carico e scarico delle materie prime in magazzino. Circa il 60% dei fornitori dell’azienda, tra cui i produttori di lastre in poliuretano, applicano il Tag già alla fonte, caricando tutte le specifiche richieste della Rinaldi per ogni singolo prodotto ordinato. All’ingresso della merce, i reader RFID leggono i Tag e tutti i dati vengono trasferiti in modo automatico nel gestionale dell’azienda, con un notevole saving di tempo da parte degli operatori. Uno step cruciale che ha permesso a Rinaldi di semplificare e migliorare la qualità totale, sia nel rispetto delle normative europee e Norme CE di riferimento, sia di tutte le lavorazioni, anche fuori formato, eseguite in conto terzi. All’inizio di ogni processo di lavorazione, infatti, viene prelevata una lastra e caricata su un primo banco di misura che, grazie ad un PLC e una centralina, dialoga con il sistema di produzione interno e verifica che le informazioni contenute nel Tag siano corrispondenti a quelle richieste, minimizzando sprechi o scarti.
Il semilavorato passa alle successive fasi di produzione. Ad ogni step, due antenne Impinj leggono i Tag e proiettano, su un monitor collocato a bordo macchina, una guida visiva di come deve essere svolta la lavorazione: ad esempio, l’incollaggio, la cucitura o una particolare personalizzazione richiesta, fino al corretto completamento del materasso. Un plus di elevato valore aggiunto, che permette non solo di abbattere ulteriormente le possibilità di errore, ma anche di rendere semplice ed immediata la formazione degli operatori e velocizzare il processo complessivo che, dall’inizio all’imballaggio finale del materasso, si attesta intorno ai 5 minuti. Le smart tecnologies di Impinj consentono, inoltre, un aggiornamento costante ed in tempo reale dei prodotti stoccati a magazzino e di quelli prelevati, per scorte correttamente calibrate. Infine, un ulteriore vantaggio è connesso al trasporto delle commesse per l’estero, vincolate all’ottemperanza di specifiche normative per lo sdoganamento, reso di facile esecuzione.
“Prendere parte a questo progetto è stato molto sfidante perchè ci ha messo alla prova nell’integrazione di queste tecnologie su diversi Sistemi Operativi, acquisendo una maggiore expertise anche in questo particolare settore.” Interviene l’Ing. Giuseppe Lallo, Amministratore Delegato di Reaktive Srl, che aggiunge: “Attualmente l’intera infrastruttura è funzionante. Stiamo eseguendo gli ultimi test sulla parte Software, al fine di verificarne la perfetta operatività. Sono molteplici le potenzialità da cui Rinaldi Group potrà trarre importanti benefici: ad esempio, i clienti dell’azienda potrebbero visualizzare, in tempo reale, lo stato della commessa. Ulteriori fasi, attualmente svolte manualmente, come la stampa dell’etichetta con il brand del materasso, potrebbero essere automatizzate creando nuove connettività IoT con le stampanti fornite dalla Rubino.” E conclude l’Ing. Lallo “Dall’analisi di tutti i dati raccolti nel tempo, potranno essere estrapolate interessanti informazioni per pianificare future azioni di miglioramento dei tempi e metodi di lavorazione.”
“Questo progetto di Smart Manufacturing dimostra come l’Internet of Things può essere protagonista nella trasformazione dell’industria italiana in industria 4.0; è stato un onore per me e il collega Riccardo Gervasi (SE BU Networking) supportare Giuseppe in questa sfida grazie alle tecnologie Impinj.” Conclude Karin Marchiori, Team Leader della BU Internet of Things.
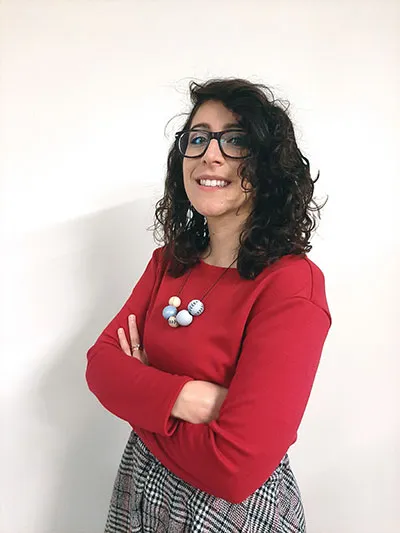
Potresti trovare interessanti anche..
Etichette per cosmetici: belle e tanto innovative!
L’Etichetta in polipropilene trasparente nella cosmetica è il supporto più usato, poiché si adatta perfettamente [...]
Le etichette personalizzate sono molto importanti per commercializzare il tuo materiale
Lo scopo di un’etichetta è quello di attrarre, un’etichetta adesiva deve convincere la mente di [...]
Instaurare un rapporto personale e confidenziale con il cliente è per noi fornire un servizio di qualità!
Vuol dire non solo rispondere nel modo migliore alla richiesta che ci è stata fatta, [...]
La particolare densità dei colori serigrafici fa si che vengano utilizzati molto spesso per impreziosire etichette che necessitano di dettagli pregiati
Siamo specializzati nella produzione di articoli per il settore agro-alimentare e vitivinicolo, ma abbiamo diversi [...]
Le etichette per l’industria dell’olio motore
sono pellicole adesive in plastica o carta ideali per l'etichettatura dei contenitori più usati nel [...]
Le etichette in bobina sono ideali per uso industriale
Hai la possibilità di personalizzare il diametro dell’anima della bobina, il verso di uscita e [...]
Rubino & Reaktive rendono digitale il processo di produzione di Rinaldi Group
Smart Manufacturing: un gioco di squadra agevolato dal Piano Nazionale Industria 4.0 Si tratta di [...]
L’effetto WOW che non ti aspetti!
Siamo attratti da colori sgargianti, ma sono i dettagli che ci portano al tanto atteso [...]